Introduction
Explanation of Sheet Metal Shearing Machines
Sheet metal shearing machines are widely used in metal fabrication industries to cut sheets of metal into different shapes and sizes. These machines use a shearing process, where a sharp blade cuts through the metal, separating it into two pieces.
Importance of Sheet Metal Shearing in Metal Fabrication
Sheet metal shearing is an important process in metal fabrication as it allows metal workers to cut metal into precise shapes and sizes, reducing waste and increasing production efficiency. The sheared edges are also smoother and more uniform than those produced by other cutting methods, making it ideal for use in high precision metal fabrication projects.
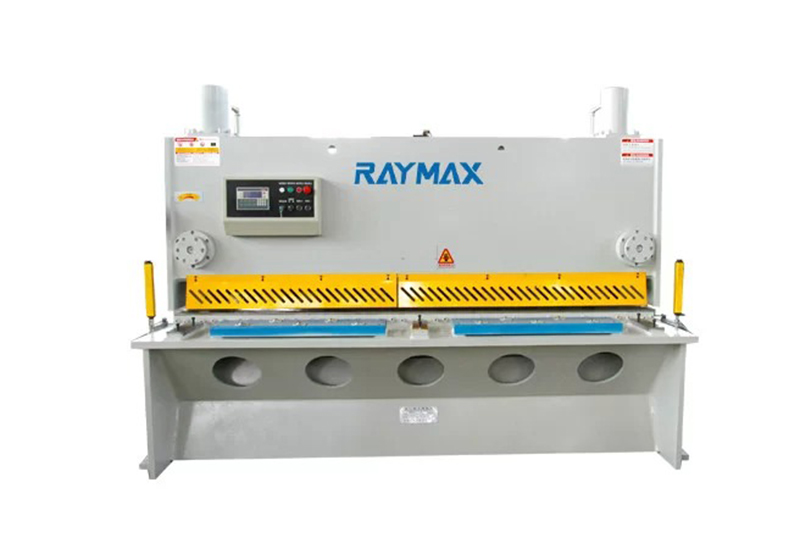
Purpose of the Blog
The purpose of this blog is to provide a comprehensive guide to sheet metal shearing machines, including their basics, advancements in technology, and tips for optimal use. We aim to educate metal workers, metal fabricators, and anyone else interested in sheet metal shearing on the latest advancements in this field, helping them make informed decisions on their machinery investments.
Understanding the Basics of Sheet Metal Shearing
Definition and Explanation
Sheet metal shearing is a cutting process where a sharp blade moves along a straight line to separate a piece of metal into two pieces. The shearing force is applied perpendicular to the direction of the cut, and the blade cuts through the metal by breaking its bonds.
Shearing Process and Mechanism
In sheet metal shearing, the metal is placed between a fixed blade (called the bottom blade) and a moving blade (called the top blade). The top blade moves along a straight line towards the bottom blade, and the metal is separated when the blades meet. The size of the cut is determined by the distance between the blades and the speed at which they move.
Types of Shearing Machines
There are several types of sheet metal shearing machines, including mechanical shearing machines, hydraulic shearing machines, and CNC (Computer Numerical Control) shearing machines. Mechanical shearing machines are manually operated and are most suitable for small fabrication shops, while hydraulic shearing machines use hydraulic pressure to increase cutting power and speed. CNC shearing machines, on the other hand, use computer control to automatically cut metal to precise specifications.
Advancements in Sheet Metal Shearing Technology
Hydraulic Shearing Machines
Hydraulic shearing machines use hydraulic pressure to increase cutting power and speed. They are equipped with a hydraulic pump that provides the necessary pressure to move the top blade and make the cut. This type of machine is highly efficient and precise, and is widely used in metal fabrication industries.
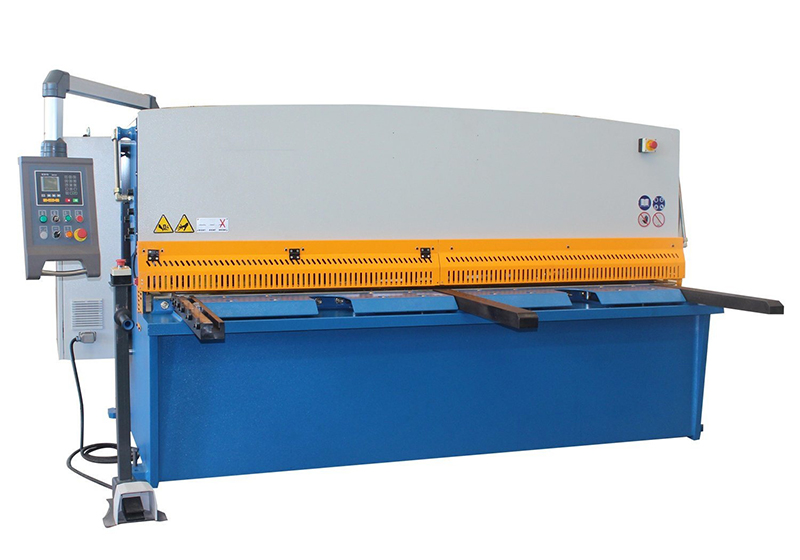
CNC (Computer Numerical Control) Shearing Machines
CNC shearing machines are equipped with computer control systems that allow for precise and automatic cutting of metal. These machines are capable of cutting metal to exact specifications and can be programmed to produce multiple cuts in a single operation, increasing production efficiency.
Servo-Driven Shearing Machines
Servo-driven shearing machines use servo motors to control the movement of the blade, allowing for precise and efficient cutting. They offer higher accuracy and repeatability compared to traditional hydraulic shearing machines.
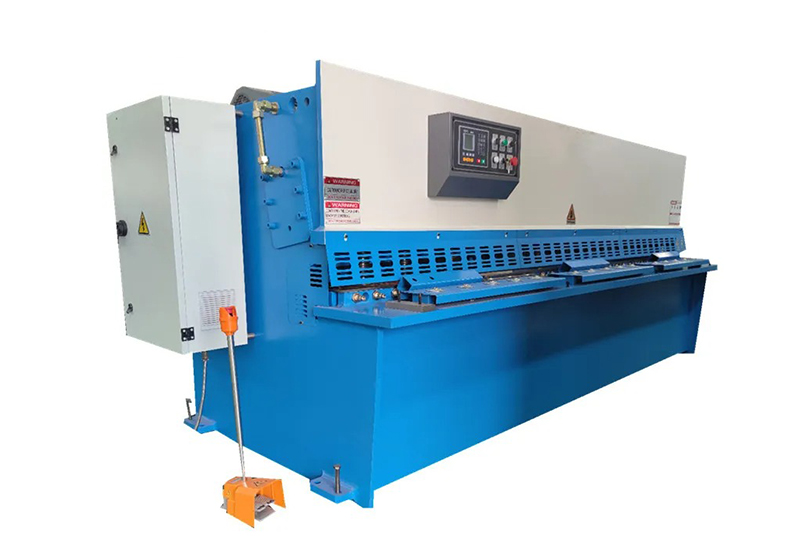
Comparison of different types of Shearing Machines
When choosing a sheet metal shearing machine, it is important to consider the specific needs and requirements of your metal fabrication process. Mechanical shearing machines are most suitable for small fabrication shops, while hydraulic and CNC shearing machines are more suitable for larger production facilities. Servo-driven shearing machines offer higher accuracy and repeatability compared to hydraulic machines, but may come at a higher cost.
Tips for Optimal Use of Sheet Metal Shearing Machines
Maintaining the Blades
One of the key factors in ensuring the optimal performance of a sheet metal shearing machine is the maintenance of its blades. The blades should be kept sharp and properly aligned to ensure that they produce accurate cuts. It is also important to regularly clean and lubricate the blades to prevent corrosion and wear.
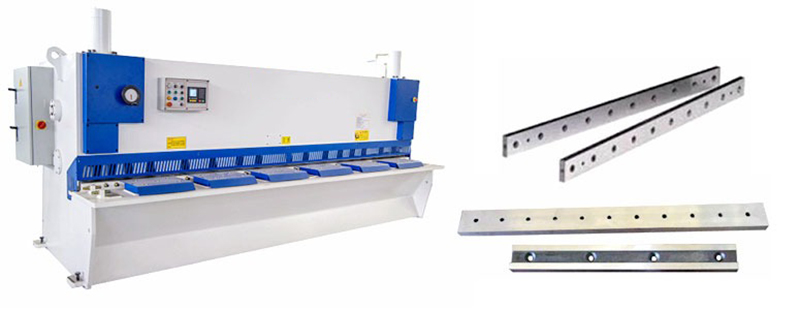
Setting the Cutting Parameters
In order to produce accurate cuts, it is important to set the correct cutting parameters on your sheet metal shearing machine. These parameters include the cutting speed, blade gap, and blade angle. The blade gap should be set to the appropriate size to ensure that the metal is cut cleanly, while the cutting speed should be set to the appropriate level to produce the desired edge quality.
Proper Material Handling
Proper material handling is also critical to achieving optimal results with a sheet metal shearing machine. The metal should be securely clamped or held in place to prevent movement during the cutting process. This will help to prevent inaccurate cuts and reduce the risk of blade damage.
Proper Training and Safety Measures
Finally, it is important to ensure that operators are properly trained and familiar with the safe operation of a sheet metal shearing machine. This includes understanding the machine's controls and safety features, as well as following proper safety procedures, such as wearing protective gear and using guards or shields to protect against flying debris.
Factors to Consider When Choosing a Sheet Metal Shearing Machine
Production Volume
One of the most important factors to consider when choosing a sheet metal shearing machine is the production volume. For small-scale production, a manual or mechanical shearing machine may be sufficient. However, for larger-scale production, a hydraulic or CNC shearing machine may be more appropriate.
Material Thickness and Type
The thickness and type of material being cut will also play a role in choosing a sheet metal shearing machine. Some machines may be better suited for cutting thin sheets, while others may be more capable of handling thicker materials. Additionally, some machines may be better equipped to handle certain types of materials, such as stainless steel or aluminum.
Cutting Accuracy and Repeatability
Another factor to consider is the cutting accuracy and repeatability of the sheet metal shearing machine. This is particularly important for applications where precise cuts are required. CNC and servo-driven machines tend to offer the highest level of accuracy and repeatability.
Operating Cost
The operating cost of a sheet metal shearing machine is another important consideration, including the cost of maintenance, blade replacement, and energy consumption. It is important to choose a machine that provides a good balance between performance and cost.
Space Requirements
Finally, it is important to consider the space requirements of the sheet metal shearing machine. Some machines may be larger and require more floor space, while others may be more compact and require less space. This is particularly important for metal fabrication shops with limited floor space.
Conclusion
Sheet metal shearing is a critical process in the metal fabrication industry, and the use of a high-quality sheet metal shearing machine is essential for producing accurate and efficient cuts. With the advancements in technology, there are several types of sheet metal shearing machines available, including mechanical, hydraulic, CNC, and servo-driven machines. When choosing a sheet metal shearing machine, it is important to consider the specific needs and requirements of your metal fabrication process, as well as the factors that can impact the performance of the machine, such as blade maintenance, proper material handling, and proper training. By following these tips and best practices, metal fabricators can achieve optimal results and improve their overall production efficiency.